Rubber tire gantry cranes (RTGs) play a crucial role in modern port operations, particularly in container handling. They provide flexibility, mobility, and efficiency in loading, unloading, and stacking containers in ports and container terminals. These cranes, known for their mobility due to rubber tires, allow operators to move them across a wide area without the need for a fixed rail system. Proper application and maintenance of RTGs can significantly enhance port operations, optimizing space and reducing downtime. This article outlines key tips for applying rubber tire gantry cranes in port operations to maximize efficiency, safety, and productivity.
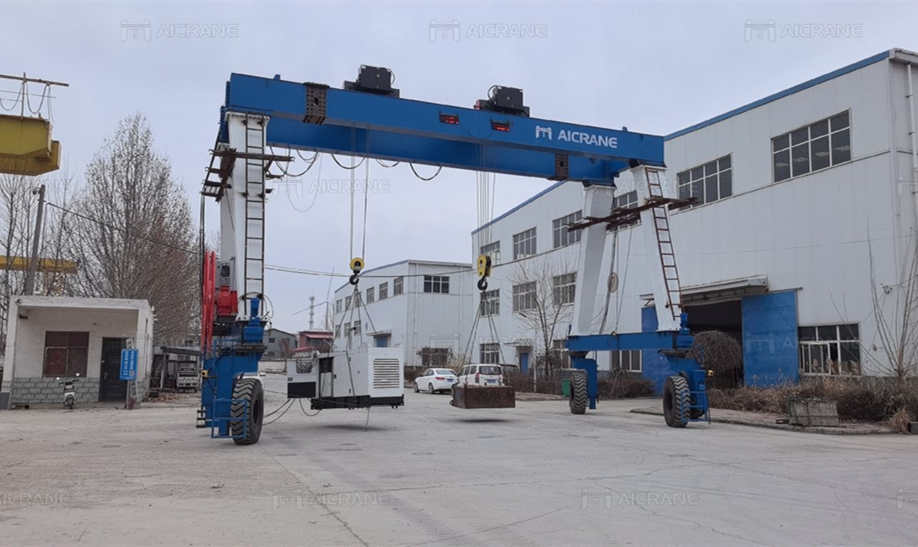
Assessing Port Layout and Container Flow
Before deploying rubber tire gantry cranes, it’s important to carefully assess the port layout and container flow. This will help determine the most suitable areas for crane operations and ensure smooth workflow without congestion.
Evaluate the Yard’s Configuration: Understand the container yard’s dimensions and layout. RTGs are ideal for ports where space is limited but still require flexibility in container movement. Ensuring that the yard layout can accommodate the crane’s movement will prevent unnecessary delays.
Traffic Flow Planning: Planning traffic flow within the container terminal is essential to avoid bottlenecks. RTGs, given their ability to move on rubber tires, offer flexibility in directing container movements. Proper planning allows them to move containers efficiently without causing interference with other equipment, such as straddle carriers or trucks.
Determine Optimal Stacking Patterns: RTGs excel in stacking containers vertically, optimizing the use of limited ground space. Plan for maximum container density, which should take into account crane height, the stacking capacity, and access to each container to reduce delays.
By thoroughly assessing the port layout and determining container flow, ports can strategically place rubber tire gantry cranes to maximize operational efficiency.
Selecting the Right Size and Capacity for the RTG Cranes
Choosing the appropriate size and capacity for rubber tire gantry cranes from manufacturer like Aicrane is critical to their success in port operations. The crane’s size, lifting capacity, and operational reach should match the specific requirements of the port.
Lifting Capacity: Depending on the type of containers being handled (e.g., 20-foot or 40-foot containers), the RTG crane should have the appropriate lifting capacity. Most RTGs are designed to lift loads of up to 40 to 60 tons. Ensure the crane’s capacity meets the needs of the port’s throughput and container type.
Height and Number of Tiers: RTGs can stack containers in multiple tiers, typically ranging from 5 to 8 containers high. Assess how much vertical space is available for stacking and ensure the crane height is suitable for maximizing the use of space in the port.
Operational Span: The span of the crane, typically covering multiple lanes of container stacks, determines how many containers the crane can handle at once. Consider the number of lanes or containers that the crane needs to straddle to ensure optimal loading and unloading efficiency.
Choosing the right size and capacity for RTGs will ensure that they can handle the port’s volume of containers efficiently without being over- or under-utilized.
Training Crane Operators for Efficient Use
To fully utilize rubber tire gantry cranes in a port, it’s essential to provide proper training for crane operators. Even the best equipment won’t deliver peak performance if the operators lack the necessary skills.
Operation Techniques: Train operators on the specific operating systems of the RTG cranes, including joystick controls, monitoring systems, and automated features. Many modern RTGs come equipped with advanced control systems, including automated container handling and anti-sway technology. Proper training ensures that operators can fully leverage these systems for faster, safer operations.
Safety Protocols: Operators must also be well-versed in safety protocols, including load balancing, movement control, and emergency procedures. Safety training reduces the likelihood of accidents, which can be costly and disrupt operations.
Efficiency Practices: Focus on efficiency by training operators to minimize downtime. Teach them how to optimize container handling through faster load/unload cycles, reduce unnecessary movements, and follow best practices for energy efficiency.
Regular training updates, as well as certification programs, ensure operators are proficient and up-to-date on the latest RTG technology and procedures.
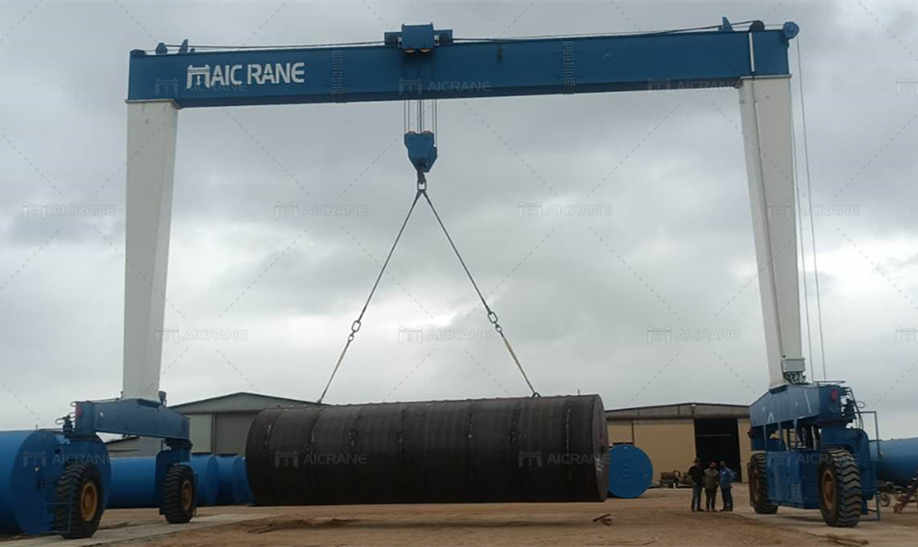
Implementing Preventive Maintenance for Maximum Uptime
Like all heavy equipment, rubber tire gantry cranes require regular maintenance to prevent breakdowns and extend their service life. Implementing a preventive maintenance program will reduce the risk of unplanned downtime and costly repairs.
Tire Maintenance: Since RTGs rely on rubber tires for mobility, regular inspection of tires is necessary. Check for wear and tear, proper tire pressure, and any damage to ensure smooth movement. Replacing worn-out tires in a timely manner can prevent accidents and reduce energy consumption.
Hydraulic and Mechanical Components: Regularly inspect the crane’s hydraulic systems, cables, and mechanical components. Lubrication, checking for wear on gears, and replacing hydraulic fluids are all necessary steps in maintaining the crane’s operational integrity.
Electrical Systems and Automation: With the increasing use of automated systems in RTGs, it is essential to monitor and maintain electrical components. This includes checking the condition of sensors, control systems, and wiring to ensure proper functioning. Automated RTGs often rely on sophisticated control systems, so maintaining these systems is critical for reliable performance.
Preventive maintenance ensures that rubber tire gantry cranes operate efficiently and helps avoid costly breakdowns or disruptions in port operations.
Incorporating Energy-Efficient Practices
Port operators are increasingly focusing on sustainability and energy efficiency. RTG cranes, especially electric or hybrid models, can help reduce the environmental impact of port operations when used efficiently.
Switch to Electric or Hybrid Models: Many modern rubber tire gantry cranes are designed to run on electric power or hybrid systems that reduce diesel consumption. These models are not only environmentally friendly but also reduce operating costs in the long run.
Energy-Saving Practices: Train operators to incorporate energy-saving practices, such as minimizing idle time and shutting down the crane when not in use. Optimizing work schedules to reduce crane idle time can also significantly reduce energy consumption.
Regenerative Energy Systems: Some RTG cranes are equipped with regenerative braking systems that convert braking energy into electricity, which can then be reused in operations. Consider investing in cranes with this feature to boost energy efficiency.
Implementing energy-efficient practices not only helps the environment but also lowers operational costs, making port operations more sustainable and profitable in the long term.
Ensuring Compliance with Safety and Environmental Regulations
Ports are subject to a variety of safety and environmental regulations, and ensuring that rubber tire gantry cranes comply with these regulations is essential for smooth operations.
Safety Regulations: Ports must adhere to strict safety standards to protect both workers and equipment. Ensure that RTGs are equipped with safety features such as anti-collision systems, emergency brakes, and load monitoring systems. Regular safety audits and inspections are necessary to maintain compliance with local and international safety regulations.
Environmental Regulations: Many countries have stringent environmental laws that govern port operations. Make sure the RTGs comply with these regulations, particularly regarding emissions and noise levels. Electric or hybrid RTGs may be required in areas with strict environmental standards to reduce emissions.
Staying compliant with safety and environmental regulations will prevent legal issues and fines, ensuring smooth and continuous operations at the port.
Optimizing Workflows with RTG Automation
Automation is transforming the way ports operate, and rubber tire gantry cranes are no exception. RTGs equipped with automated systems can significantly improve the efficiency and accuracy of container handling.
Automated Container Handling: RTGs with automation systems can quickly identify, pick up, and place containers with minimal human intervention. This reduces human error, improves precision, and increases the speed of container handling.
Remote Control Operations: Some RTGs are designed to be operated remotely, allowing operators to control multiple cranes simultaneously from a central control room. This can reduce labor costs and increase the overall efficiency of the terminal.
Data Integration and Analytics: Modern RTGs are equipped with sensors that collect data on crane performance, container movements, and energy usage. Ports can use this data to optimize workflows, predict maintenance needs, and improve overall operational efficiency.
By embracing automation, ports can use rubber tire gantry cranes more effectively, reducing labor costs and improving container handling speeds.
Rubber tire gantry cranes are essential tools for port operations, providing flexibility, mobility, and efficiency in container handling. By carefully assessing the port layout, selecting the right crane size and capacity, training operators, implementing preventive maintenance, incorporating energy-efficient practices, ensuring regulatory compliance, and embracing automation, ports can optimize the use of RTGs. These best practices will not only enhance productivity but also reduce downtime, operational costs, and environmental impact, making ports more competitive in the global logistics landscape.